Overview of Services
Continuous Process Improvement Services
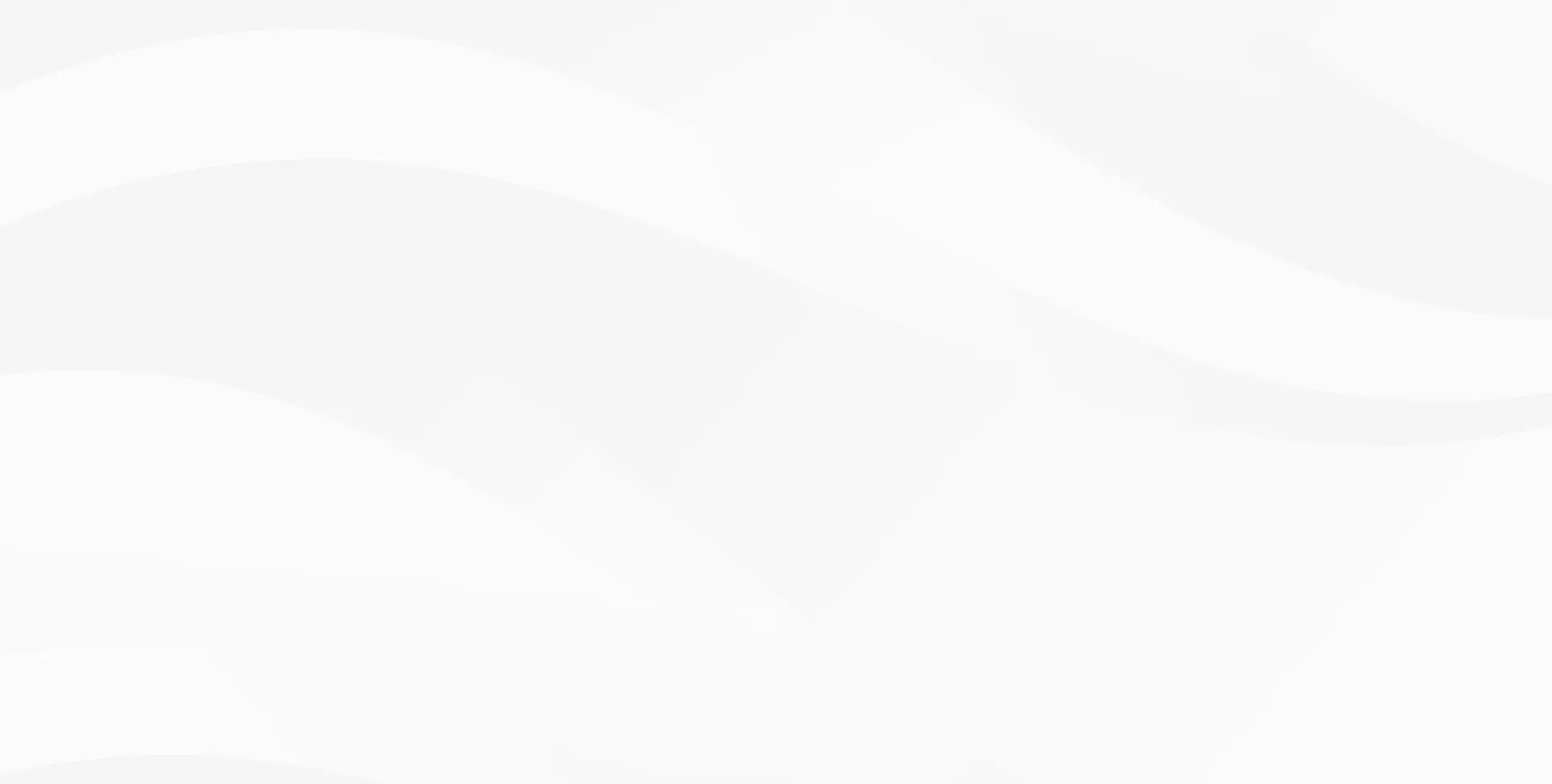
Process Improvement & Optimization
- Value Stream Mapping (VSM):Â Identifying inefficiencies in workflows and finding ways to remove waste.
- Process Standardization:Â Creating best practices for repeatable and efficient operations.
- 5S Implementation:Â Organizing workplaces for efficiency (Sort, Set in Order, Shine, Standardize, Sustain).
- Kaizen Events:Â Facilitating structured problem-solving workshops to drive rapid improvements.
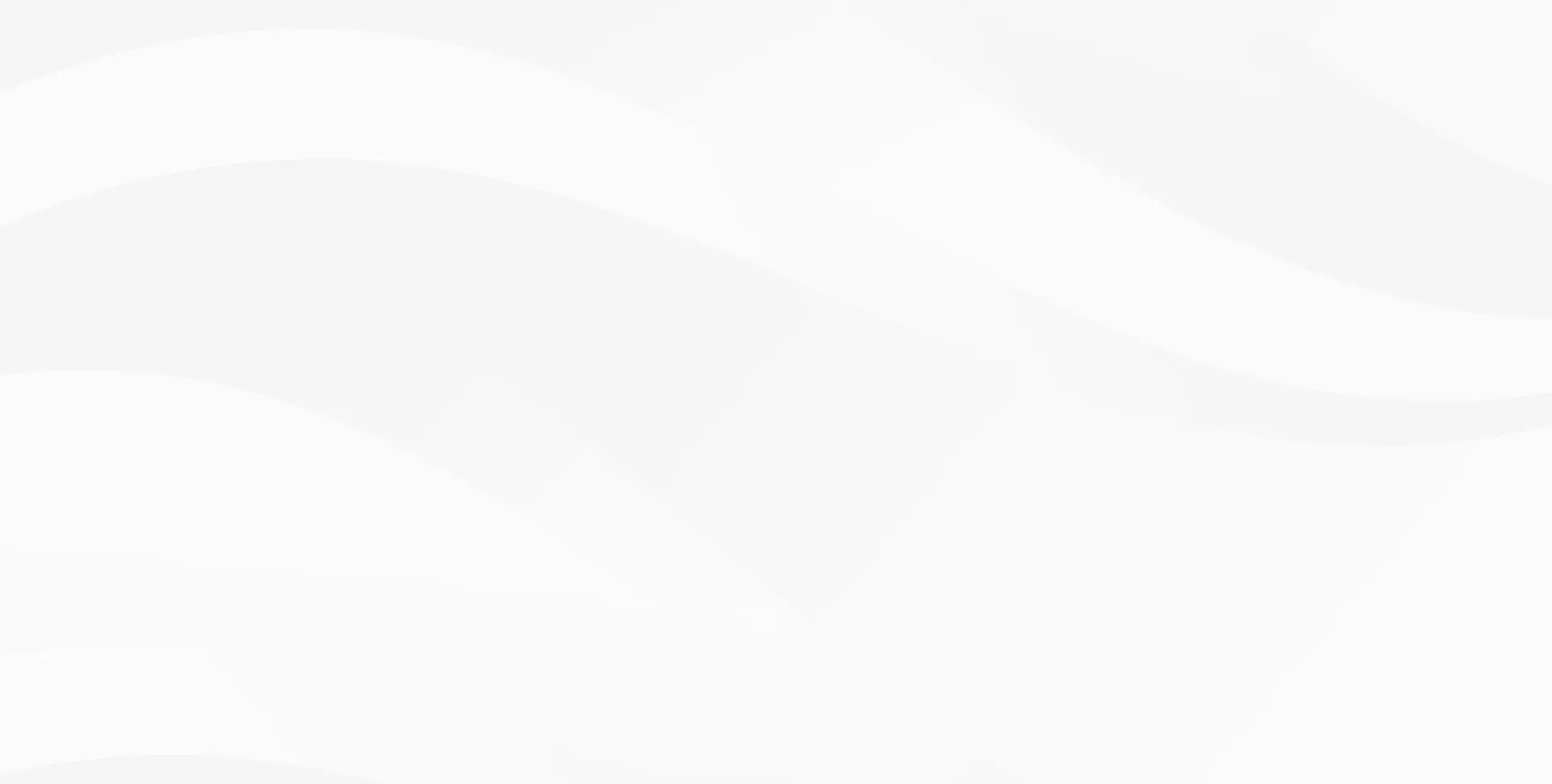
Operational Excellence & Cost Reduction
- Lean Assessments:Â Analyzing current processes and identifying opportunities for cost savings.
- Waste Reduction (TIMWOOD+E):Â Eliminating waste (Transportation, Inventory, Motion, Waiting, Overproduction, Overprocessing, Defects, and Employee underutilization).
- Cycle Time Reduction:Â Improving speed and throughput while maintaining quality.
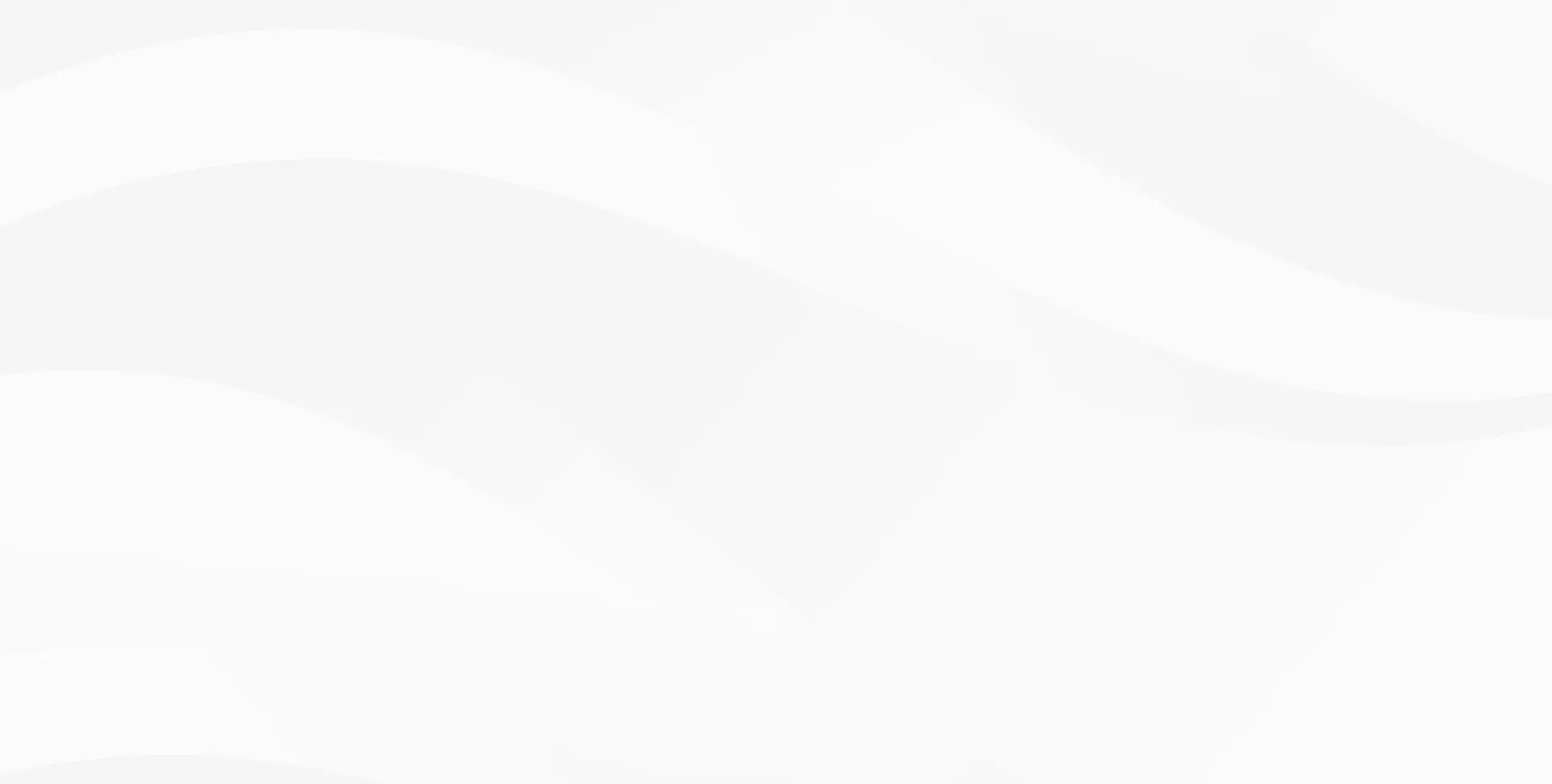
Lean Leadership Development
- Lean Mindset Training:Â Teaching leaders and employees how to think and act with a continuous improvement mindset.
- Gemba Walks:Â Coaching leaders on how to observe work where it happens and engage with employees for improvements.
- Daily Management & Problem-Solving Culture:Â Implementing structured routines for continuous monitoring and problem-solving.
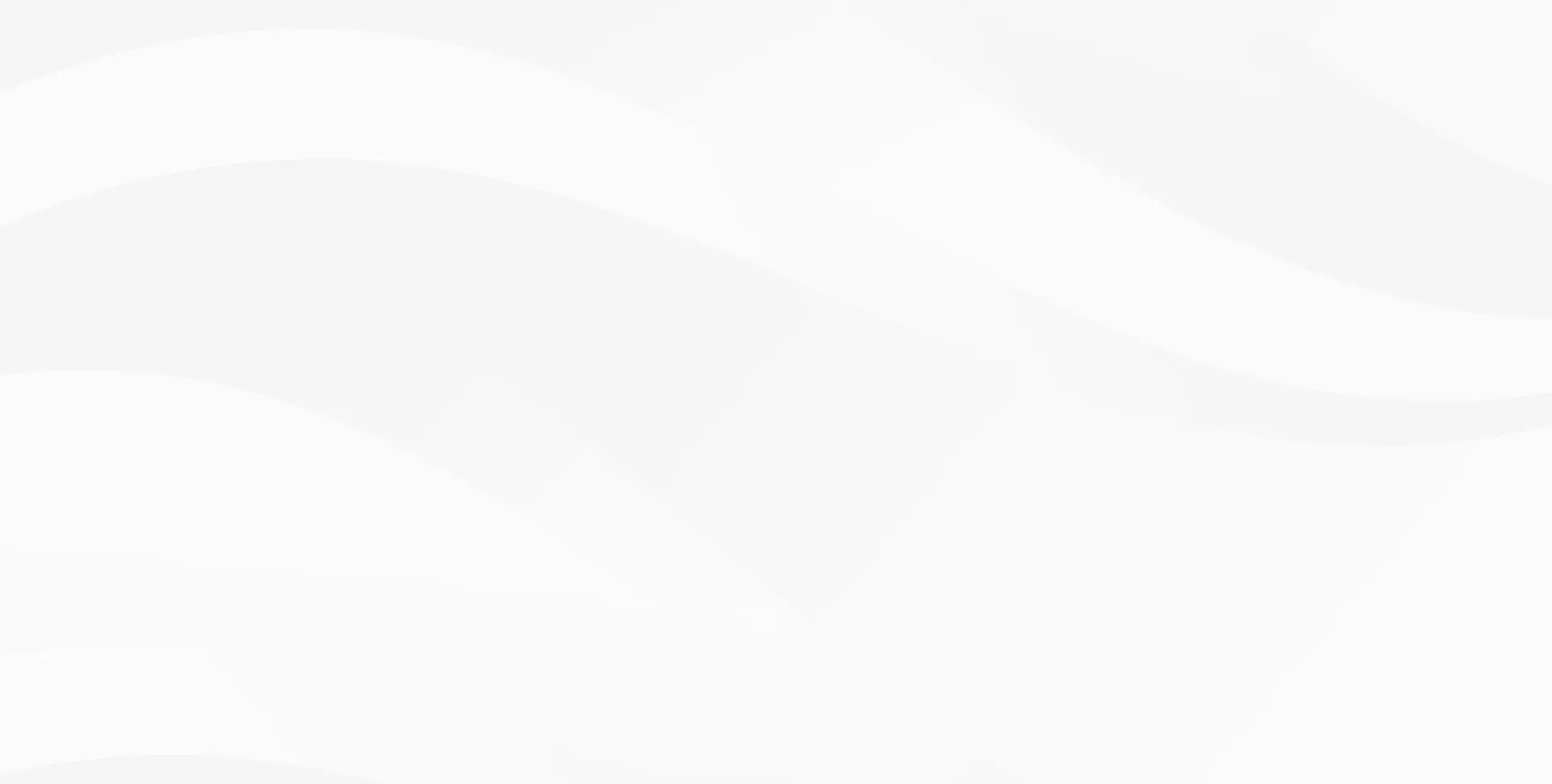
Performance Measurements & Data Analytics
- KPI Development & Dashboarding:Â Defining and tracking key performance indicators to measure success.
- Root Cause Analysis (RCA): Using tools like 5 Whys, Fishbone Diagrams, and Pareto Analysis to identify and fix recurring problems.
- Statistical Process Control (SPC):Â Applying data-driven methods to ensure process stability and quality.
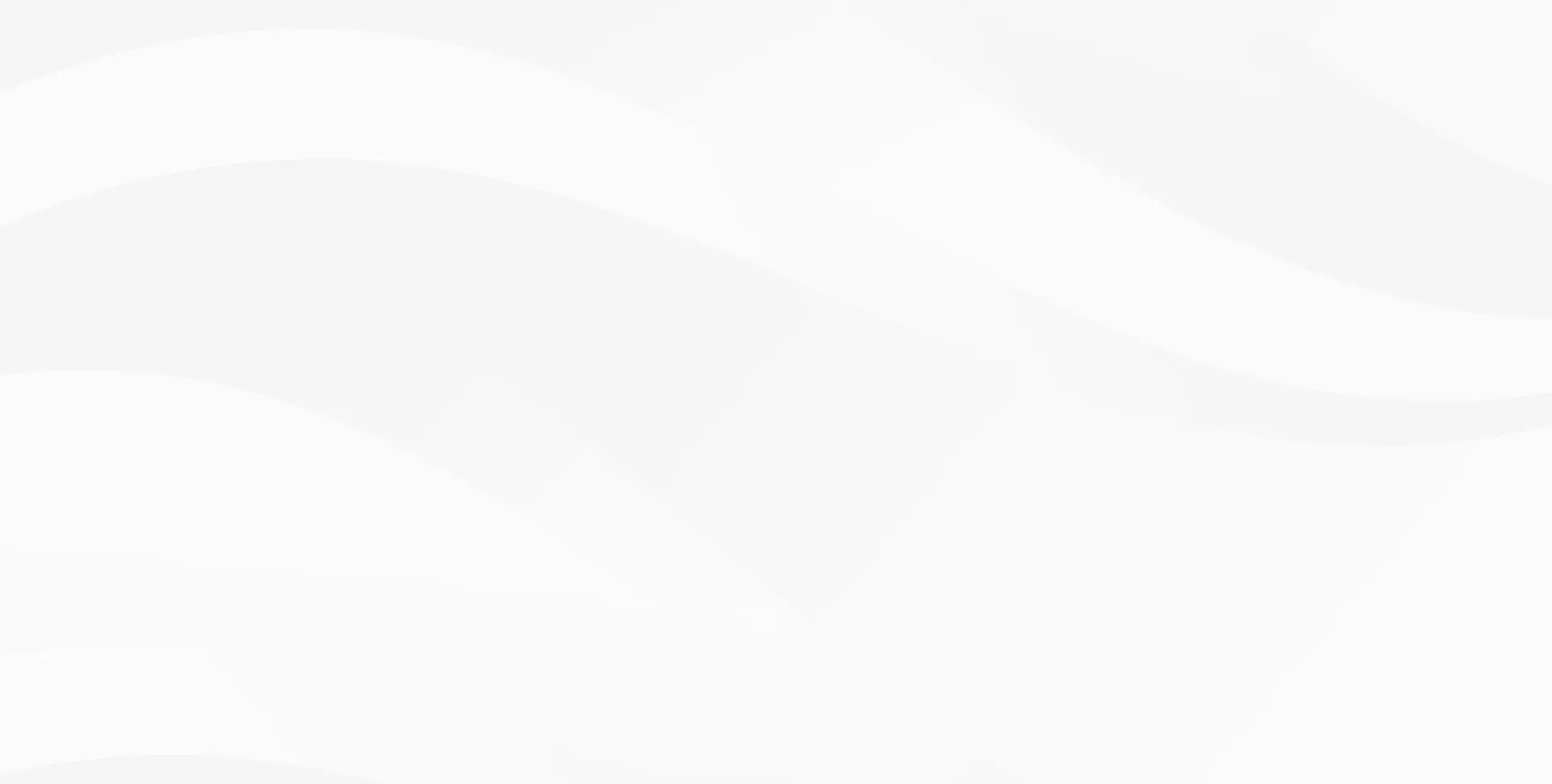
Lean Digital Transformation
- Process Automation & Workflow Optimization:Â Streamlining repetitive tasks with technology.
- AI & Data Analytics for Continuous Improvement:Â Using data-driven insights to enhance decision-making.
- Integration of Lean & Industry 4.0:Â Applying Lean principles to modern digital tools (IoT, AI, Smart Manufacturing).
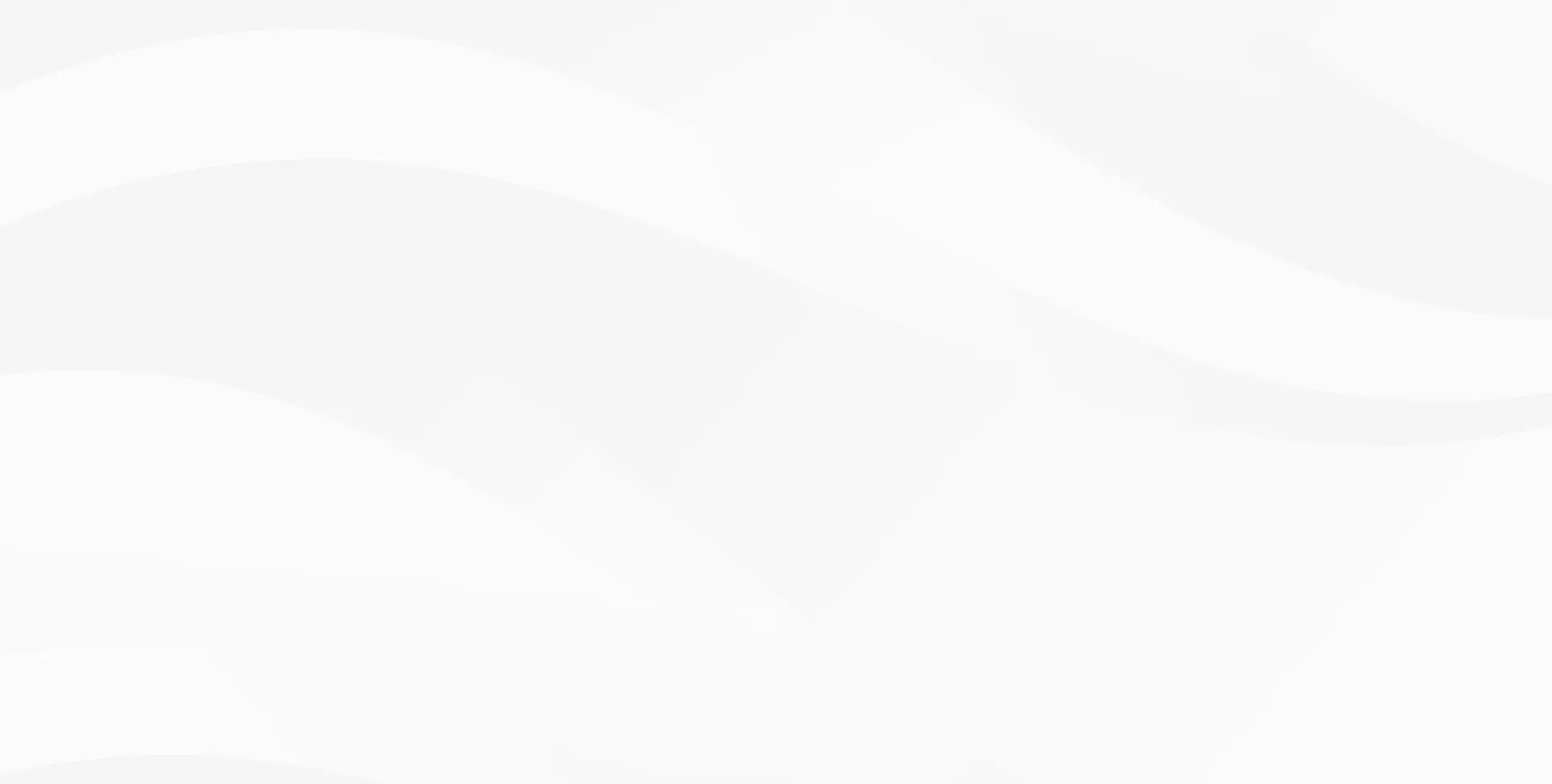
Change Management & Employee Engagement
- Lean Coaching & Training Programs:Â Educating employees at all levels on Lean principles and techniques.
- Employee Engagement Strategies:Â Ensuring frontline workers contribute to and sustain continuous improvement.
- Leadership Development for Lean Transformation:Â Equipping executives and managers with the skills to lead change.
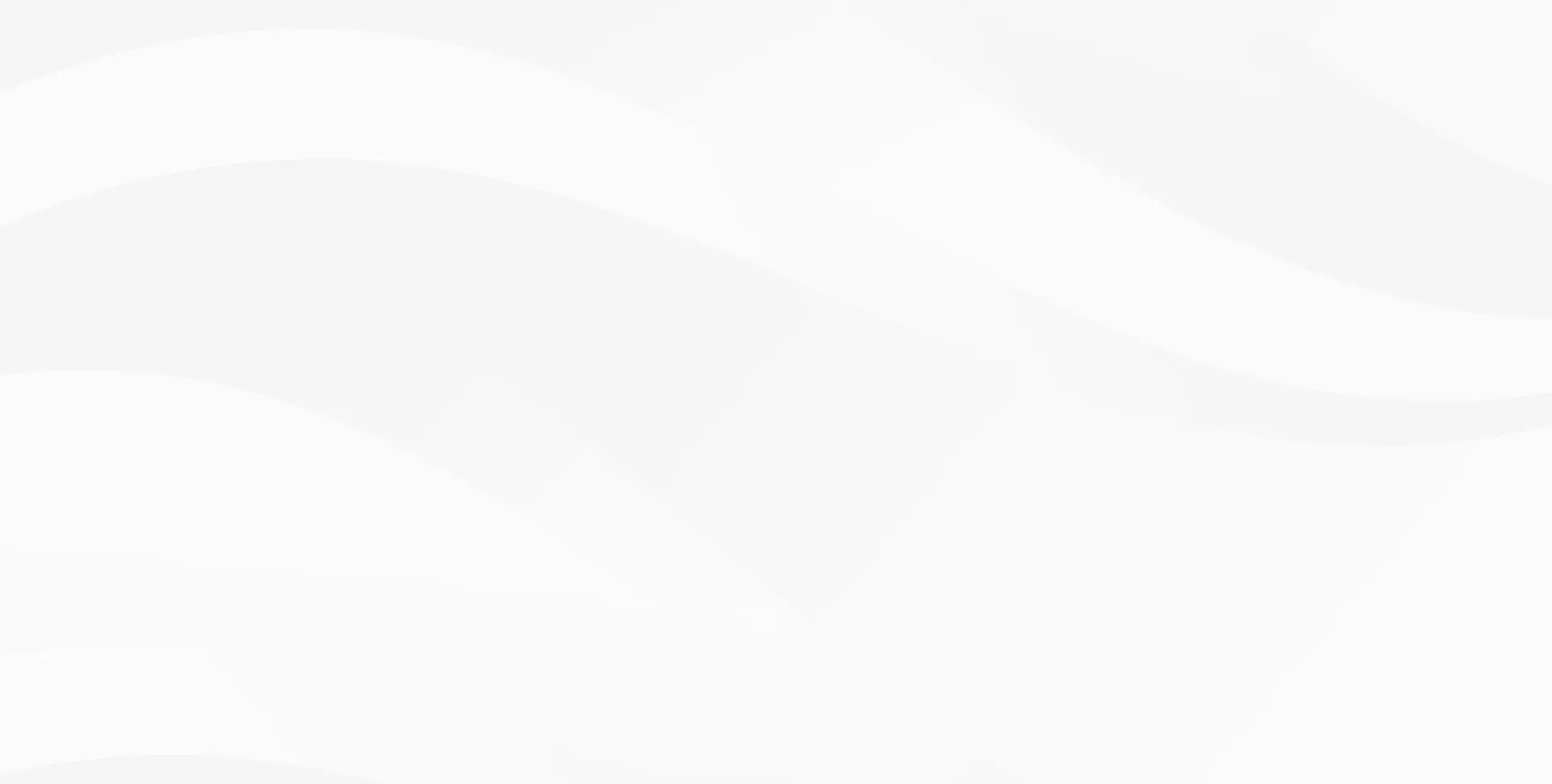
Custom Solutions Based on Industry Needs
- Manufacturing:Â Reducing machine downtime, improving production flow, and implementing Lean Six Sigma.
- Supply Chain & Logistics:Â Optimizing inventory management, warehouse operations, and distribution efficiency.